
Sustainable heating & cooling for a high-rise building
Case study on efficient heating and cooling in an office building
BerlinBerlin is a vibrant metropolis that is preparing for a sustainable and environmentally friendly future. One example of this is the new East Side Tower, which connects the lively and artistic districts of Friedrichshain and Kreuzberg. The East Side Tower was carefully built with a focus on sustainable practices, from the use of recycled products and VOC-free materials to world-class energy management that uses chillers for sustainable heating and cooling.
GOT ANOTHER EXCITING PROJECT?
Be sure to let us know!
Requirements:
- High comfort
- Low operating costs
- Small ecological footprint
- Maximum efficiency
- Smart control
Background
SustainabilityEDGE East Side – one of Germany’s most sustainable high-rise buildings
Located centrally just a few metres away from the metro station at Warschauer Strasse, the EDGE East Side Berlin is one of the most sustainable high-rise buildings in Germany. Measuring 142 m in height and with over 65,000 m2 of office space, it has become an iconic part of the Berlin skyline. The building is characterised by its innovative and open architecture, designed by Bjarke Ingels Group (BIG). It combines contemporary urban requirements with natural elements, creating spacious rooms that invigorate visitors and passers-by alike and invite them to enter. Amazon will be the largest tenant in the building, taking up 28 of the EDGE East Side’s 36 floors. The project was completed in 2023.
The high-rise building is one of the first projects of its kind to meet the city’s new guidelines for these structures in many aspects. The EDGE East Side is a smart, sustainable building in which the offices not only fulfil a function, but are also part of the surrounding community. The Berlin city construction committee was involved in the project to ensure the quality of the architecture and urban planning. This helped the building to meet the stringent requirements for construction quality, sustainability, health and comfort. The EDGE’s reputation for quality is underlined by a platinum pre-certificate from the German Sustainable Building Council (DGNB) and the aim to be awarded the WELL v2 Core & Shell Gold certification of the International WELL Building Institute. Key to meeting these benchmarks is the heating and air conditioning solution.
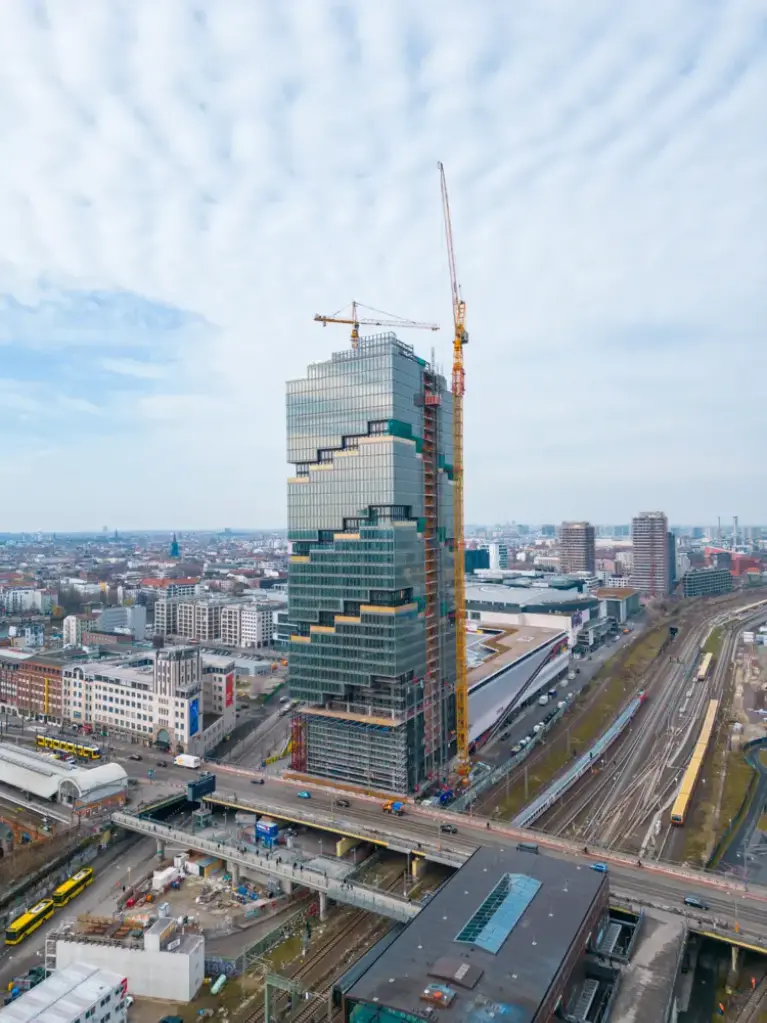
What were the requirements for the building’s air conditioning?
RequirementsAn energy-efficient system for a small ecological footprint
The building offers top-class energy management, constantly optimising itself through networked technology and automatically supporting both energy efficiency and user comfort. The light and temperature settings, for example, are adjusted locally and heavily used areas are ventilated more based on usage data. All tenants have direct access to the building’s intelligent functions. A mobile EDGE app, for example, allows users to control the light and temperature. Constant analysis and adjustment of technical processes maintains continuous compliance with sustainability goals. A central part of the sustainability strategy and energy management is the building’s energy system.
The main requirements in this modern multi-purpose building were to provide comfort while reducing operating costs and keeping the ecological footprint as small as possible. These demanding specifications are met by means of an intelligent system design that controls the temperature in the building via two central ventilation systems with heat recovery, a connection to the city’s district heating system, and four air-cooled chillers. The system uses four outdoor chillers from Climaveneta, a Mitsubishi Electric brand. These feature inverter-controlled type i-FX-G05 screw compressors with cooling capacities between 599 and 842 kW. The i-FX series is designed with sustainability in mind, achieving the efficiency levels necessary in this project and therefore supporting the developer’s forward-thinking approach.
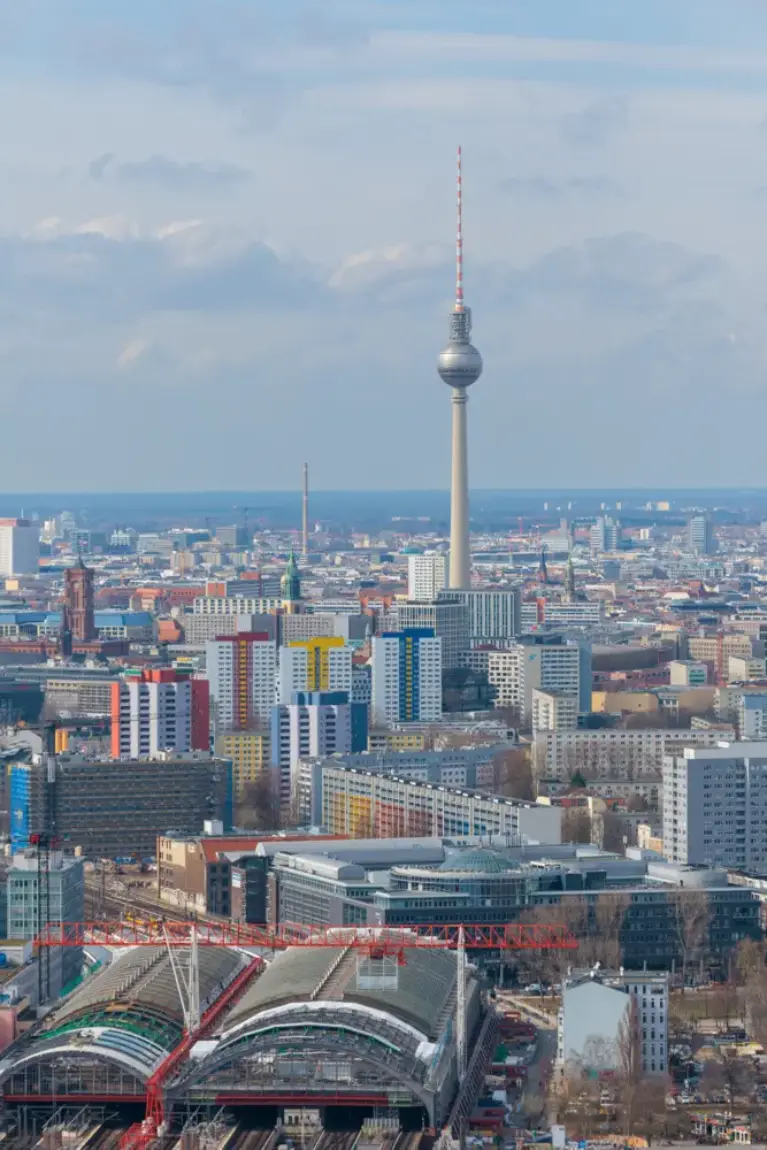
Which solution was chosen for the high-rise building?
ChillersInverter-controlled chillers from Climaveneta, a Mitsubishi Electric brand
The air-cooled chillers meet the need for ever greater comfort alongside reduced operating costs and a minimal ecological footprint like no other unit series in this performance class. Weighing between 6,700 and 9,700 kg, the units were raised by a crane onto the roof of the building 142 metres up and brought into position in just three hours. The delivery and installation of the units while construction operations were still ongoing was a logistical masterstroke that was possible thanks to Mitsubishi Electric staff on site as well as those of Apleona Wolfferts GmbH, a specialist company for building and HVAC technology.
The four chillers deliver a total cooling capacity of around 2.7 MW and fulfil various tasks. The two “smaller” units, each delivering around 600 kW of cooling capacity, are connected to the room air systems and supply the two ventilation systems with the necessary cold. They can therefore reliably pre-condition the supply air as required. The central ventilation units are responsible for the fresh air supply and controlled exchange of air, as well as covering the base load for the required room heating or thermal load dissipation (cooling). When the need for heating is greater, the heat is provided either via the local district heating network or from the heat recovery of one of the four chillers installed on the roof.
The other two chillers, which deliver 830/842 kW of cooling capacity, are used for direct cooling in the rooms across the total of 36 floors. This occurs via so-called ceiling sails, which are used for both heating and cooling. Suspended freely in the room, the ceiling sails enable high heating and cooling capacities, as well as offering outstanding noise absorption. They are also the ideal solution for the demanding architectural requirements of the building. They offer a view of the bare ceiling thanks to their open design, as well as a large degree of design and arrangement freedom when dividing up the room.
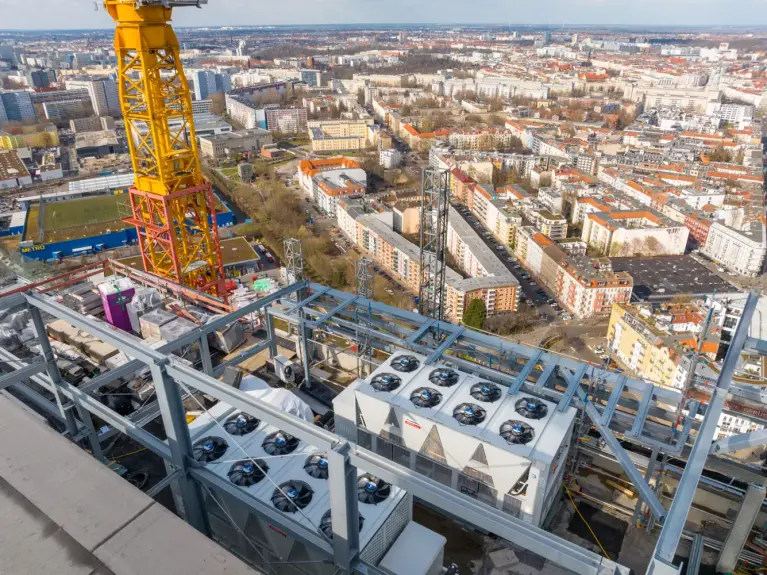
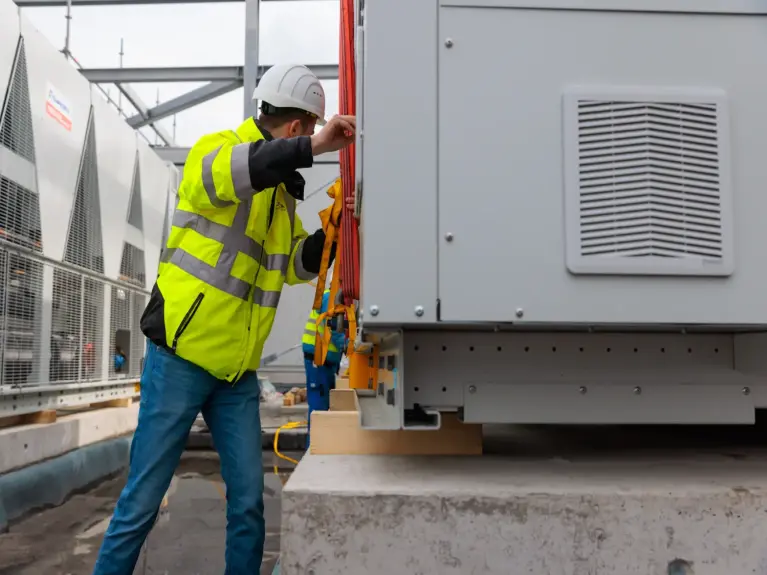
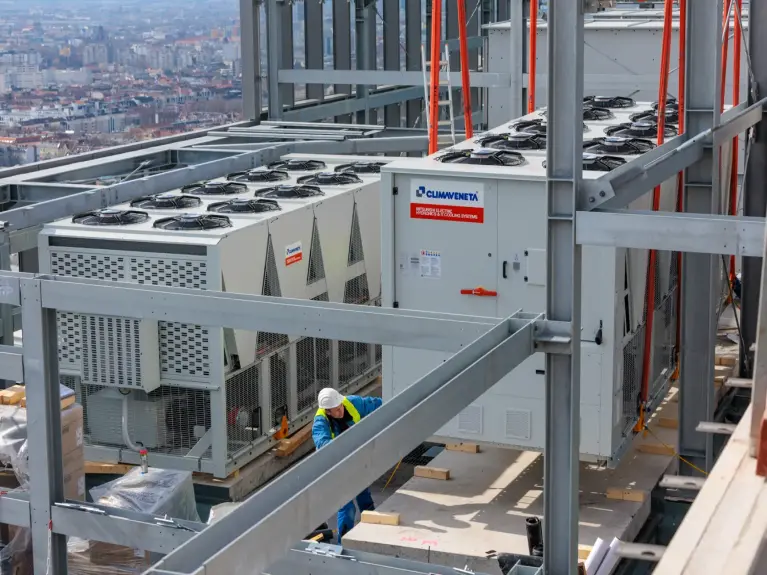
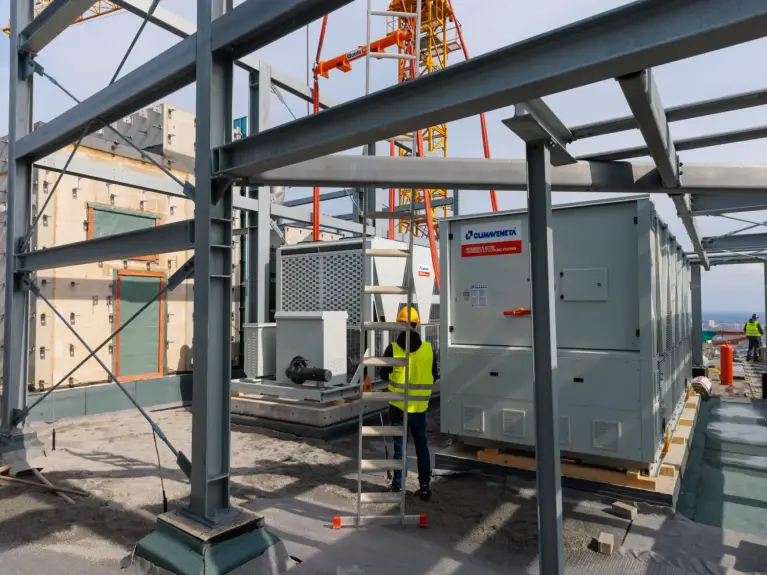
Sustainable environmental management with heat recovery
The most powerful of the four chillers on the roof is worthy of special mention. This has a heat recovery function that is used to charge a buffer storage tank in the basement. A heat recovery system retains the heat drawn from the rooms during cooling in the system instead of releasing it into the environment. The heat is conveyed via the buffer storage tank to the various substations and heating circuits, before being distributed into the rooms via the ceiling sails. With a heat recovery rate of 100%, the system is incredibly efficient. It reduces operating costs, encourages sustainable environmental management and was a major factor behind the building’s environmental certification.
Reduced environmental footprint
A variety of configuration options and equipment features allow the units to be perfectly integrated into the overall sustainable concept of the building. The inverter-controlled screw compressors are a good example of this. By enabling precise control, they allow the system to work particularly efficiently under partial load. This is because in addition to the reliable provision of chilled water, energy efficiency in the medium partial load range plays a major role in comfort air conditioning applications.
On top of this, the i-FX-G05 is specially optimised for the use of environmentally friendlyR513Arefrigerant. R513A has a GWP that is 56% lower than that of R134a. It is also completely non-toxic and non-flammable (ASHRAE 34 – class A1, ISO 817). Despite this, it offers similarly good thermodynamic properties to R134a and guarantees high energy efficiency. This combination of top-class efficiency and the use of a low-GWP refrigerant allows the chillers to aid in the fight against direct and indirect global warming thanks to their very low primary energy consumption.
Intelligent control
The chillers are controlled by the software W3000+ and KIPlink interface, which can be connected easily to the existing building control system. The W3000+ control has auto-adaptive temperature control for faster adaptation to a wide range of load requirements and optimised fault diagnostics with a “black box” function. For on-site operation, a large LC display with self-explanatory function keys is available for quick and easy enquiry and adjustment using a multi-level menu.
The control system offers cutting-edge functions and algorithms, as well as settings options that quickly adjust the units to the conditions in all operating modes. The system can be controlled directly via the innovative KIPlink interface. As it uses a local WLAN network, KIPlink allows users to work on the system directly via a mobile device such as a smartphone, tablet or laptop.
The key points
Summary- The EDGE East Side in Berlin is one of Germany’s most sustainable high-rise buildings, setting benchmarks in construction quality, sustainability, health and comfort.
- To meet the demanding requirements, the building uses four air-cooled type i-FX G05 chillers with inverter-controlled screw compressors from Mitsubishi Electric.
- The four chillers deliver a total cooling capacity of around 2.7 MW and fulfil various tasks in the system.
- Thanks to a wide range of configuration options, like the heat recovery function in one of the four chillers, they can be perfectly integrated into the building’s sustainable technology concept.
- With a heat recovery rate of 100%, the system is incredibly efficient. It reduces operating costs, encourages sustainable environmental management and is a major factor behind the building’s environmental certifications.